Specialists in creating beautiful, healthy, low-energy homes.
Lomas and Mitchell Architects specialise in low-energy buildings, with a particular fondness for private residential projects. We love helping our Clients to make the most of their properties.
We are really excited to share our latest project, first broadcast on Grand Designs on Wednesday 28th September 2022.
This modern interpretation of a Derbyshire Longhouse is only some solar-shading (and external works) away from completion. Borrowing much from the agricultural barns already located on this small-holding, the profiled cladding on the walls and roof are refined versions of those familiar materials in the landscape. The (yet to be installed) vertical fins echo the ‘hit and miss’ timbers found on many barns, offering shading from direct sunlight.
This is one of our Paragraph 80 successes, and we have been privileged to work with a group of like-minded professionals to deliver this project. (Paragraph 80 refers to a specific clause in planning legislation which allows one-off dwellings to be built in the countryside.)
Every project starts with a conversation – do call and see how we can help you realise your dream home.
Help, when you need it.
Jillian has created a Masterclass video called “Briefing your Architect: using the Brief to help you create your dream home.” It lasts about 25 minutes, it’s easy to follow and takes you through the project work stages, looking at how you can use your Brief to keep on track.
We’ve created a free pdf to download which accompanies the video – you can download it here
Send download link to:Download your Masterclass pdf here.
A Lomas and Mitchell Architects Masterclass.
If you missed the video, it will be available here soon.
We will only use your email to enable you to download the pdf file and to send you one further email about how you can subscribe and continue to receive useful project-related information. We will never share your personal information with anyone and will never sell your details.



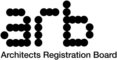
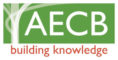
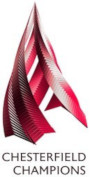